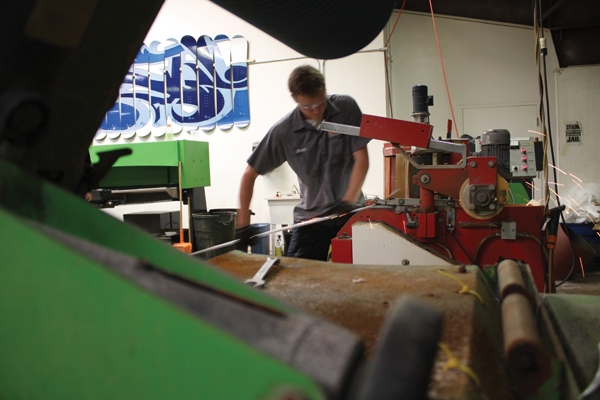
Freedom of Choice: Revolution Manufacturing
Ski / Snowboard
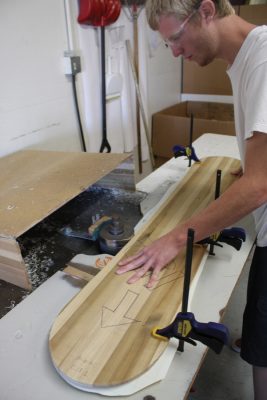
Starting in a warehouse in Orem, Revolution has been in the building business for almost seven years. Over the course of the past few years, business has steadily grown, thus allowing Revolution to be a fully in-house operation. This means that nothing in their board construction is assembled elsewhere. From start to finish, the factory has complete control over the process, allowing them to not only be comprehensive and hands-on, but also to have one of the fastest turnarounds in the business. On average, the factory is able to fulfill an industry order in about a month. One of Revolution’s most unique processes, and the one that I had the opportunity to take part in, is their Build-a-Board process. This allows the consumer the complete freedom to design their very own board, from the art to the shape to the core, these fully customizable boards will be kicking ass all over the mountain for years.
For my snowboard, I recruited the help of an old friend and artist, Rory Stack. With little notice, Rory was able to come up with some clean graphics. Design in hand, I drove down to the factory where I was greeted by the head of marketing, Matt Pinnell. After a brief introduction, we were off to start building. Our first stop was the art department where Tyler Fox would bring our design to life. “Whatever you want to do, I can make it happen,” he told me. After some fine-tuning, the images were printed out on the super printer (think personal printer just 40 times larger). Revolution offers two ways to have graphics transferred, screen print or sublimation. I chose to have my graphics sublimated (or heat transferred). This process results in a better quality than the cost-effective screen printing technique. Once the graphics were transferred to the top and bottom sheets, they were cut then placed on a template and routed.
After the art aspect was completed, we headed into the core room. Many manufacturers receive cores from an outside source––not Revolution. In this room, planks of poplar and aspen are glued and cut to make cores. Once cured and stripped, a computer cuts the core to match the correct size. Armed with my graphics and my core, it was off to have my board assembled in the largest area of the factory the construction area. This area consists of several stations: cap construction, sidewall construction, fiberglass, press area and finishing.
Revolution has a different technique when it comes to the construction of the boards’ edges. I can’t say much about it, but I can tell you that John Mon takes a very hands on approach to make sure that the edges are perfectly constructed and not going to separate from the board’s sidewalls. Once the edges are done, it’s time to add the second most important part of the snowboard, the fiberglass. Pinell explained it like this: “Think of the board as a body, the core is the bones or the skeleton and the fiberglass is the muscles.” At this point, I met up with Jordan Thurston who showed me the difference in the glasses used. We went with a 19 oz. biaxial glass to give the board more flex and reduce weight (more park specific). A thicker, triaxial glass will make for a stronger, less-flexible board, more proficient for a big mountain feel. To make sure it wasn’t too soft, we add a few strips of carbon fiber to the tip and tail area.
Now we have our basic board built in layers: base, sheet of glass, core, another sheet of glass then the top sheet. What’s different from other manufacturers is the amount of options that the Build-a-Board process offered. They have different presses for pretty much any camber (bend or shape) you want, recently adding the ability for what Pinell says is “huge now but eventually [going] to be a dying fad,”–reverse camber. We kept mine classic, however. I’m not sold on the whole reverse camber gig myself. We called it a day to let the hydraulic heat press cure the resin and let it cool so we could assure top quality.
Bright and early the next morning, I arrived to see my board completely constructed. I was amazed at how they were able to sandwich together my designs, a core and some fiberglass to make such a life changing vehicle. Though we were not quite done, the board still had some finishing processes to go through. Protective eyewear back on. After an hour of dry and wet grinding, routing the sidewalls and drilling out the inserts, the board was finally ready for its detailing through the Discovery car wash (picture automated car wash for a snowboard). This machine marks the completion of the process, as the base gets stone ground and waxed, and the edges are sharpened. After a thorough inspection and touch up by James Hulett, the board is then bagged and ready to be shipped (or just handed to me).
Being a part of the building process is unforgettable, and having a fully customized board is special. It’s awesome to see that a company like Revolution is able to exist in this industry of ever growing giants. For, as Matt Miller, CEO says, “We’re here for the love of what we do, not to build our wealth.” While other companies are selling out to bigger corporations outside of the snowboard world, Revolution is on a steady path to bringing “freedom of choice to the consumer,” something that appears to be dying every day.
Thanks to all the Revolution employees for taking the time to walk me through this process. Also, thank you to Rory Stack and Ben Rose for the all work done converting art to design.
Revolution also offers custom skateboards, long boards and wake boards. Visit revolutionmfg.com to see what the boys are up to and design your own board.