Métier Vélo – Building Momentum: A Look at Four Local Bicycle Craftsmen
Art
The creative talents of the greater cycling community convened in Salt Lake City this spring for the North American Handmade Bicycle Show (NAHBS) to showcase works of rideable art. Motivations and designs differ greatly across builders, but their passion for the sport is as hearty as the materials they choose for their stately steeds. Riding through the streets of SLC, it is often difficult to spot a handmade bicycle from afar, so take a closer look with four locals—Sixth Law Cycles, Saltair Cycles, Reynolds Cycling and Métier Vélo—who are constructing these two-wheeled dream machines
Métier Vélo
Jamie White
metier-velo.com
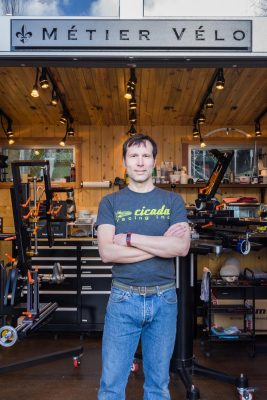
SLUG: Briefly describe the backstory behind your brand.
Métier Vélo: After 11 years and thousands of applications looking for a job in my field (molecular and cellular neurogenetics), I decided to make my own job. After much consideration, I decided framebuilding fit my meticulous personality and passion for cycling. I founded Métier Vélo in 2013, and I began to develop frames constructed with 3D-printed titanium lugs (joints) and carbon fiber tubes. I began full-time production in 2015. Making frames with titanium lugs and carbon tubes is still a novel construction technique; to date, I am the only builder using it to craft full-custom bicycles in all styles. My frames are unique in that they are not just made-to-measure for each rider, but entirely designed from the ground up, down to the smallest detail.
“Métier” means profession, in the sense of craft or calling. “Le Métier” is how professional cyclists refer to the total commitment required to race for a living: The Profession. The name of the company—Métier Vélo LLC—refers to me finding my calling, pays tribute to the racing heritage of my frames, and recognizes the total commitment required to be a professional bicycle designer and framebuilder.
SLUG: Why did you decide to choose Salt Lake City as your home base?
Métier Vélo: I was waylaid after coming to the University of Utah for a postdoctoral fellowship. SLC is an easy place to get stuck, especially living in Emigration Canyon.
SLUG: How do you engage with the local cycling community in SLC?
Métier: I race with Cicada Racing Inc. and I ride a lot. The phrase “cycling community” makes it sound like cyclists are a homogeneous bloc. In reality, there are all sorts of different types of riders and different reasons for riding. I see every type of rider in Emigration Canyon from clear beginners on their first ride to seasoned, famous professionals. If you’re passed by a rider in the Canyon, she could be an Olympic medalist.
SLUG: How many people work within your company, and how do you plan to grow your business?
Métier: One human (me), two cats (office and shop), and two dogs. I might get another cat. My goal is 24 frames per year. I won’t expand beyond that. The best builders work alone.
SLUG: What is the most difficult part of building a bicycle or components by hand?
Métier Vélo:
- Finding clients.
- Designing. My frames are designed from scratch for each client, and the 3D printed lugs leave little room for error. Each design needs to be completely accurate, and I need to model every detail before the final print.
- Bonding. The joints between the titanium lugs and carbon tubes need to be meticulously prepared and executed. The epoxy must completely coat both surfaces (lug and tube) and penetrate the bond. My scientific background was helpful in establishing protocols for maximum bond strength.
SLUG: What have been some of your biggest triumphs as a builder?
Métier: Triumph might be an overstatement. Just running a small business is hard, regardless of the business, so I am proud of myself for sticking with it.
As far as framebuilding goes, I’ve established a great collaboration with Tim Crossman in Ukraine. He is a framebuilder who also fabricates custom tubes. Tim had done some exclusive designs for Métier Vélo and we should have more cool things coming up in 2017.
Professionally, showing at NAHBS was a significant achievement. The overall level of craftsmanship and professionalism at NAHBS is high and gets higher every year. Being accepted to exhibit frames as a builder at the show validates my work and effort, and is recognition of my assembly methods, fabrication skills and designs.
SLUG: How do you attract potential customers?
Métier:
- Directly through my website: metier-velo.com
- Media attention from the NAHBS and Bespoked U.K. handbuilt bicycle shows. Don Walker, NAHBS founder and president, is almost single-handedly responsible for the renaissance in custom bicycles made by small, independent custom builders.
- Social media: Instagram @MétierVélo, FB: MétierVélo and I’m on Twitter @MétierVélo. Info from Métier Vélo is collected under #MétierVélo.
SLUG: How do you set yourself apart from other custom builders in the area and abroad?
Métier:
- Construction: No other full-custom builder uses 3D printed titanium lugs and carbon tubes with the toughened, bonding technology I employ.
- Aesthetic: My lugs have flowing curves and custom artwork printed right into the lugs. My lug designs have shapes that can only be fabricated by 3D printing. Tim Crossman’s tubes have a unique woven look. Together, the 3D-printed parts and custom tubes create a look that pays tribute to classic lugged frames.
- Design: I don’t just cut tubes to measure; I design every aspect of the bicycle from the ground up in 3D modeling software.
- Versatility: I make all styles of bicycle, limited only by what a client and I can envision.
- Durability: My frames have a lifetime, no-questions-asked guarantee. Well, I’ll probably ask some questions. And the lifetime is my lifetime, not yours.
SLUG: Tell us about your 2017 NAHBS experience. Was it your first show or have you been going for a while?
Métier: NAHBS 2017 in SLC was great. Métier Vélo had a primo location and we had good media exposure. Because I was local, I ended up being interviewed on KRCL and the KSL morning show. I’ve been going to NAHBS since the 2014 show. Don Walker and NAHBS are largely—maybe entirely—responsible for the resurgence of custom bicycles built by small independent builders like Métier Vélo. Don and NAHBS set the bar very high for the level of craftsmanship and professionalism, and because framebuilders are a competitive bunch, the average level of framebuilding at the show increases every year.
SLUG: Why did you decide to use 3D printing as a fabrication solution for frame building?
Métier: 3D-printing lugs is really well-suited to building custom bicycle frames for several reasons:
- Scale: The unit of economy is a build volume—the maximum volume a 3D printer can print in one go. The parts for a single frame fit efficiently into a single-build volume. Beyond one volume, there is no economy of scale, so 10 frames cost 10 times as much as one. Since they can all be different at no cost penalty, they might as well all be different, which means full-custom is the only strategy that makes sense.
- Tolerances: 3D-printed parts are amenable to hand finishing, one part at a time, because they have lower tolerances than machined parts. The lower tolerances mean that it is does not make sense to manufacture large batches of uniform parts. The flip side is that I am not at a disadvantage hand-finishing one frame one at a time, so I am not competing with high-throughput assembly-line manufacturing.
- Design freedom: 3D-printed lugs can have smooth, continuously variable shapes with no internal structures (or, alternatively, complex internal structures). 3D-printing frees me from the manufacturing constraints of machined parts.
- Value: 3D-printing is relatively expensive, but the high cost is justified when it is used to produce a bicycle unique for each individual that will last a lifetime.
- Toughness: The 6/4 titanium used in 3D-printing is aerospace grade and will outlast the carbon on the frame. And probably the rider. And definitely the builder.
- Repairability: In the case of a crash, I can cut the carbon tubes apart and re-cycle the lugs. The carbon tubes are relatively cheap, so this repair strategy makes sense.
- Ride: The lugs are very strong and stiff, so the ride quality of one of my frames is determined primarily by the carbon tubes and the way they are bonded to the lugs. For the bonds, I use epoxy with a bit of elasticity, so high-frequency vibration does not propagate through the frame to the rider. The resulting ride is really smooth.
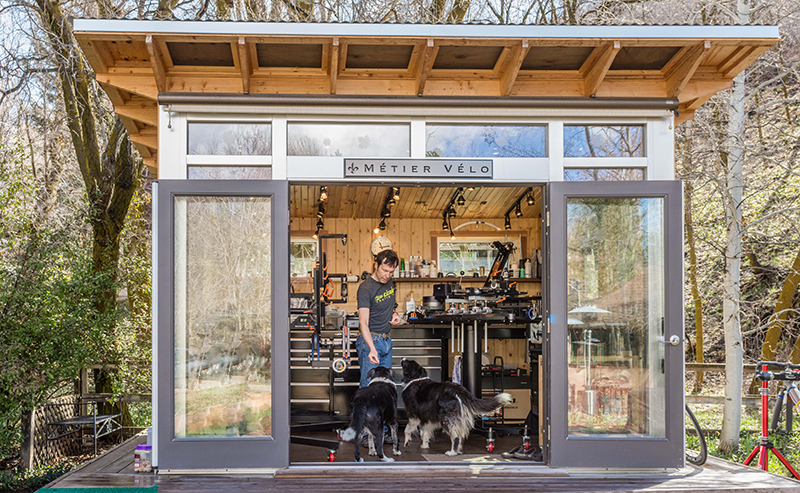
SLUG: Has this always been your method, or have you used other techniques to build a frame?
Métier: Always. I have only built frames with 3D-printed titanium lugs and carbon tubes.
SLUG: How many bicycles have you built since starting your business, and which one stands out as your favorite?
Métier: Eight. I was severely injured by a hit-and-run driver in 2016, so I am a bit behind where I would like.
The best frame is always the next one. Although the last one is pretty nice: It is a classic rim-brake road bicycle with some custom tubes developed in collaboration with Tim Crossman. I call it the Super622. If you are a chemist who owns a Cannondale, you’ll get it.
SLUG: Your shop is your art space. How does this influence your design and process overall?
Métier: Most of my framebuilding time is spent designing in CAD software on the computer. I have a nice office space with a desk companion (Sophie the cat) and the dogs. When contemplating a new career, the first and often the only question you need to ask is, “Can I have my dogs at work with me?”
When I am fabricating a frame, I need calm and quiet in order to concentrate. The workshop provides a tranquil space that lets me focus on the task at hand. Framebuilding also requires problem-solving, and the peaceful setting of the shop encourages contemplation and clear thinking. From one window I can see memorials to two friends that died in 2016. They catch the afternoon sun and remind me of the transience of existence.
SLUG: What motivates you to continue building frames, and what changes might you implement in the future?
Métier:
Motivation:
- Enthusiasm. I am really excited about cool things. It is really motivating to implement new ideas for cool bicycles to build and ride. Back when I first started riding, there was one type of frame—road—and two kinds of components—Shimano or Campagnolo. Now there are so many different options for a bicycle, only a few of which you can buy from a shop—disc brakes, wide tires, fat tires, road bikes, gravel bikes, all-road bikes, cyclocross bikes, mountain bikes, fat tires, plus tires, small wheels and so on—that a custom build really makes sense. And if you can’t make sense of it all, a custom builder can really help. You can have a bike made just for you in so many ways—not just the frame, but in style and function.
- Riding. I am fond of my bicycles—not just the ones I’ve designed and built, but the ones I’ve ridden over the last 35 years—because of the places they have taken me and the experiences they have allowed me to have and the ways riding has enriched my life. Riding is therapy as much or more than training. It is really rewarding to make something that enriches someone’s life, and make him or her healthy and sane.
- Fear. Total, utter, all-consuming fear. Failure is not an option. I am on Career Plan Z. At this point in my life, there is no fallback option. No one will ever hire an over-educated, middle-aged white guy with dubious social skills.
Changes:
- Tech. There are design improvements enabled by 3D-printing and improvements in CAD software that I would like to implement. The improvements I have in mind involve designing lugs with internal lattice structures inspired by nature.
- Decoration. I’d like to add a bit of color to the tubes and lug details. I am not a fan of paint because riders worry about chipping it and so avoid riding on some really great roads. I’m experimenting with different surface treatments of the lugs and tubes.
- Cost. Because of the initial cost of the 3D-printed lugs, my first frame cost over $12,000. In the past two years, I’ve managed to decrease this by optimizing my designs and working with several different prototyping companies. Currently, my least expensive frame is $5750 when purchased with a full bicycle, a price lower than many other high-end builders. I hope to continue to work on costs to bring better value to my clients.